
Nincs még tökéletes megoldás a modern ipar legégetőbb problémájára
Általános iskolai történelemóra, 1784, gépesített szövőszék - nagyjából innen számítjuk az ipari forradalmat, amikor a kézi munkát elkezdték leváltani a gépek. Most pedig a negyedik forradalomnál tartunk – ezt hívják Ipar 4.0-nak – aminek, a korábbiakhoz hasonlóan megvannak a maga problémái.
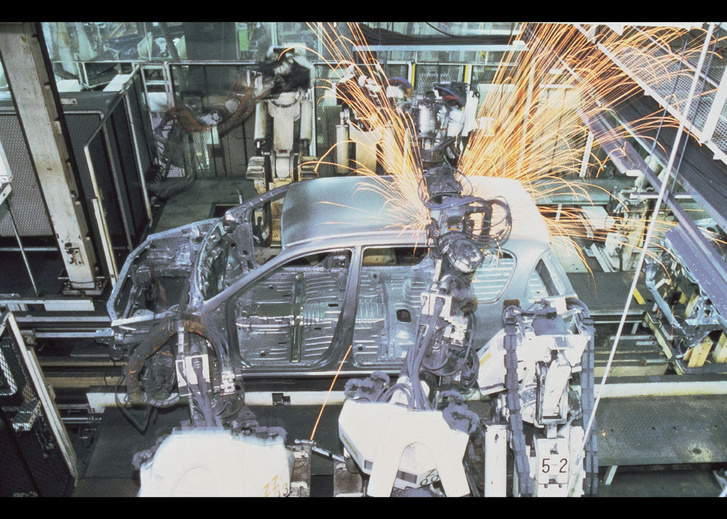
A Szövő Jenny és a teljesen automatizált, hálózatba kötött gyártási folyamatok között volt két fontos lépés, a második ipari forradalom néven emlegetett esemény a gyártósor megjelenése volt - bár a történelem leghíresebb gyártósora a Fordhoz köthető, de nem az volt az első. 1870-ben egy vágóhídhoz köthető a legkorábbi, ismert gyártósor kialakítása, akkor jelent meg a ma is ismert rendszer, amelyben minden egyes munkás csak egyetlen munkafázist végez. A harmadik ipari forradalmat – az első Holdra szálláshoz és a Led Zeppelin első albumához hasonlóan – 1969-re teszik a történészek, ekkor jelent meg az első PLC (programozható logikai vezérlő, ez még nem számítógép, de majdnem, bizonyos folyamatok irányításáról való, könnyen programozható, villamosan működő vezérlő), ami elhozta az ipari robotok első hullámát. A most zajló negyedik forradalom keretein belül a gyártásban résztvevő gépeket hálózatba kapcsolják, így azok egymással kommunikálnak, sőt, szükség esetén akár döntéseket is hozhatnak.
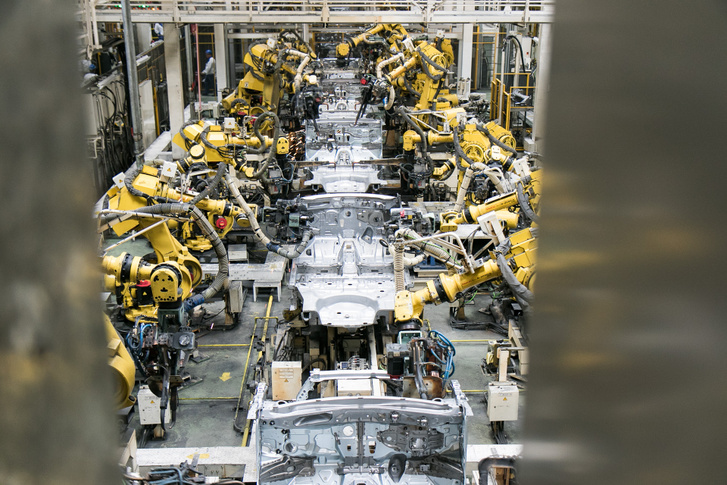
Mielőtt elfelejtenénk, ezekre az ipari forradalmakra azért volt, illetve van szükség, mert a vásárlói igények és a fogyasztói szokások folyamatosan változnak, fejlődnek. A vevői igények változása ugyanakkor csak egy az ipari forradalmakat kiváltó számos tényező között. A legfontosabb vásárlói érték az autók tömeggyártása, amit sorozatgyártásnak hívunk. Régen, amikor még nem voltak gyártósorok, akkor még egyedi gyártásról beszéltünk, magas hozzáadott értékű emberi munkatartalommal. A kizárólag megrendelésre készített termékeket egyedi igény szerint gyártották és kevesen tudták megfizetni azokat. A gépesítés, a Ford által bevezetett tömeggyártás tett széles körben elérhetővé és megfizethetővé számos terméket, amit a robotok használata tovább bővített. Ezeknek a technológiáknak köszönhetjük, hogy világméretűvé vált az autógyártás és az autózás is.
Bár maga a hálózatba kapcsolás elsőre nem tűnik olyan átütő forradalomnak, mint a gépnek a feltalálása, de általánosan elfogadott nézet, hogy pont a hálózat az, ami túlmutat önmagán. Nagyjából ugyanaz a helyzet a gépekkel, mint az idegsejtekkel, önmagukban nem sokat érnek, viszont összekapcsolva őket egy új dimenzió nyílik meg - idegsejtekből összeáll az emberi agy, a számítógépek tömegéből pedig az internet. A hálózat pedig képes arra a fajta adatgyűjtésre és rendszerezésre, amivel például az önvezető autó jobbá válhat az emberi sofőrnél: a tudását nem határolja be az egy élet alatt levezethető kilométerek száma, hanem az összes hálózatba kötött autó összes kilométeréből tanul - és egy halálos baleset sem jelenti a tanulási folyamat végét, hanem újabb, fontos információkkal szolgál, amelyek alapján legközelebb az önvezető rendszer már kivédheti ugyanazt a szituációt.
Elméletben oké, de hogy néz ki a gyakorlatban?
Elméletben oké, de hogy néz ki a gyakorlatban? Ahhoz, hogy lássuk, hol tart ma a technológia, a 4iG ipari digitalizáció szakértőjét, Virág Aladárt kérdeztük meg, aki húsz év autóipari tapasztalattal a háta mögött konkrét példákkal tudja bemutatni az autógyártás átalakulását.
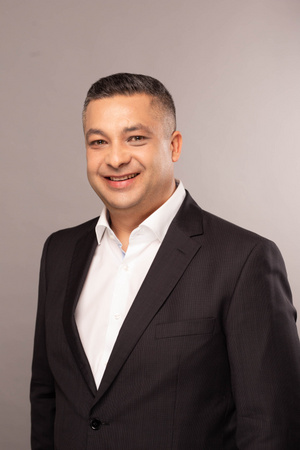
"Az embert azonban nem szorította ki a gépesítés, hanem tovább fejlesztette és szorosabbá tette az együttműködéseket többek között az úgynevezett diszruptív és formabontó technológiákkal, mint például a kevert valóság (Mixed Reality, MR), vagy a mesterséges intelligencia (MI és artificial intelligence: AI). Az 5G hálózati campus a gyárakban lehetővé teszi a vezeték nélküli kommunikációt gépek, robotok és szoftverek között. Ezen technológiára kapcsolva az eszközöket kinyílnak a fejlesztési lehetőségek, akár az önműködő targoncák (AGV) kommunikációja, akár az önvezető autók és forgalomirányítási eszközök irányába. A hálózatba kapcsolt automata targoncákat használják a gyárakban – a moduláris gyártást lehetővé tevő AGV-k már 1973-ban jelen voltak a Volvo Kalmar gyárában is, kiváltva ott ezzel a futószalag rendszerű gyártást.
Várhatóan a közutakon is járhatnak hamarosan az önvezető autók, amik reagálnak a külvilág érzékelhető jellemzőire, s mivel hálózatba vannak kötve, így egymással is kommunikálnak. Legutóbb, egy autóalkatrész gyártó információja szerint, a BMW olyan önvezető autókon is dolgozik, hogy a hátsóülésen ülve egy 80 x 20 cm-es kijelzőn keresztül képesek legyünk közben egy konferencián is részt venni. A prémium gyártók úgy gondolkoznak, hogy ne csak az autóik legyenek innovatívak, hanem a gyárak és a gyártási folyamataik is, ahol ezek a prémium autók készülnek.
A felhőtechnológia is komoly szerepet kap a jövőben. Autógyártásunk körülményeit az erre feljogosított cégvezetők egy kattintással megnézhetik akár a mobiltelefonjuk kijelzőjén is: a világ bármely pontján van is az a gyárunk, sőt, az is látható, melyik gyártósor milyen teljesítménnyel működik. A felhőalapú online monitoring rendszerrel sokkal részletesebb adatok alapján, gyorsabban, egyszer hozhatók meg a döntések. A felhőrendszereken az autók használat közben is információkat oszthatnak meg önmagukról a többi közlekedőnek, a szerviznek, a flottakezelőnek, a biztosítónak, vagy az autókereskedőknek és persze a gyártóknak is - az élő használati adatokból levonható tapasztalatok pedig visszacsatornázhatók a termékfejlesztésbe.
Mondanám, hogy ez még jövő, azonban ez már masszívan a jelen, a gyártásban használják a felsorolt technológiákat. A gyártósorról most legördülő termékek már nem pusztán autók, hanem mobil számítógépek magas intelligenciával és jelentős kommunikációs képességekkel. Leegyszerűsítve annyit mondhatunk a modern autókról: vasba csomagolt szoftver, ami négy keréken gurul.
Súlyos dollármilliók múlhatnak ezen, vagyis nem csak egy általános szerszámtörés okozhat a beszállítói láncban gyártási problémát, hanem ma már a gyártási informatika zökkenőmentes működése számít a legfőbb kritériumnak. Eddig csak a sci-fi és The Fast and the Furious filmekben láthattunk olyat, hogy egy drón képes a levegőből kinyitni egy autót. Nincs is annyira messze, mert megtörtént a Tesla X modelljével, hogy egy közönséges DJI Mavic 2 drón egy wifi modemmel felszerelve az autó közelébe repült, és kinyitotta annak központizár-egységét. Ez a példa is azt mutatja, hogy a kiberbiztonság mennyire fontossá vált az autóiparban.
A XXI. századi autók négy keréken futó operációs rendszerek és alkalmazások egysége, ezért nagy veszélynek vannak kitéve a kibertámadásokkal szemben. A teslás ajtónyitás egyszerű példája annak, hogy mennyire sérülékenyek lehetnek az ilyen rendszerek, de az autótolvajok „munkájának” megkönnyítésén felül nagyobb gondot is okozhat a biztonsági réseken behatoló, az autó haladásába illetéktelen beavatkozó (sebesség vagy fékezés befolyásolásával) emberéleteket is veszélybe sodorhat."
Ahogyan az összes ipari szintlépésnél voltak pro és kontra érvek, mindegyik felvetette a maga politikai, filozófiai és technológiai problémáit, kezdve az alacsonyan képzett munkaerő jövőjétől az új technológiákat övező szkepticizmusig. Elég csak a ludditákra gondolni, egyetlen nagy átállás sem megy zökkenőmentesen. Az Ipar 4.0-nak is megvannak a maga kihívásai, amelyek közül a biztonság a legégetőbb.
Oké, vannak gondok, de mi lesz az előnye?
- Kevesebb humán munkaerőre lesz szükség, ettől javul a gyártás rugalmassága, gyorsasága és pontossága.
- Ezzel párhuzamosan az emberek által hozzáadott munka hatékonysága, minősége javul, hiszen monoton feladatok helyett kreatívabbakkal foglalkozhatnak a dolgozók.
- A hatékonysággal párhuzamosan jobban nyomonkövethetővé válik a termelés, ezzel együtt a teljes gyártási láncban résztvevő raktárkészlet és energiafelhasználás nagyban csökkenthető.
- A végén lesz egy gyorsabb, jobb minőséget előállító, kevesebb selejtet gyártó rendszer;
- és ami a legfontosabb: mindez olcsóbban.
Jelenleg a hálózatok és az automatizáltan működő rendszerek biztonsága az egyik legforróbb téma, nem csak a gyártásban, hanem a bankszektortól a kutatás-fejlesztésig mindenhol. A biztonság alatt két külön fogalmat értünk, egyszer ott van a rendszer stabil működése (pl. lefagy a számítógép és resetelni kell), ezt hívják Safety-nek, a másik pedig a rendszer védelme, ezt angolul Security-nek nevezik. Jelenleg az utóbbi, a hálózatként működő, automatizált rendszerek biztonsága az egyik legkomolyabb aggály. Amikor egy vírussal le lehet állítani egy teljes szektort, akkor ez kiemelten fontos, illetve nem csak az a kérdés, hogy mennyire feltörhető egy ilyen rendszer, hanem hogy mennyire stabil a működése.
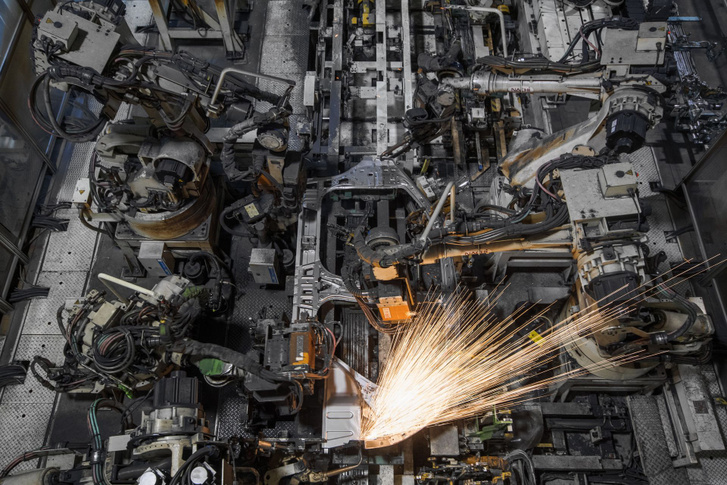
Magyarországon is előfordult már több alkalommal is, hogy első szintű, a gyártókkal közvetlen műszaki és kereskedelmi kapcsolatban álló autógyári beszállítókat (Tier 1), elektronikai gyártókat támadtak meg zsaroló vírussal, ami 3-4 napra leállította az üzemet. A gyártósor hálózatának leállása miatt a gyártás leblokkolt és egyszerűen nem lehetett újraindítani. Gondoljunk bele, hogy mit okozhat egy ilyen kimaradás a gyártási láncban:
- A vevő autógyárat, autógyárakat (az OEM-eket, Original Equipment Manufacturer) nem szolgálja ki a beszállító, vagyis leáll az adott alkatrészt tartalmazó autók készítése, a megrendelő piaci vásárlóknak a várakozási ideje megnő és több gyárban is feltorlódhatnak az autók.
- A Tier 1 üzemnek beszállító (Tier 2) gyártónak szintén le kell állnia, mert az alkatrészeire átmenetileg nincs igény.
A rendszerek sérülékenységére remek példa a Stuxnet vírus, amelyet az iráni atomprogram ellen vetett be az USA és Izrael. A feladata az volt, hogy tönkretegye az iráni kísérleti atomlaborban működő urándúsító centrifugákat. A Stuxnet azért is volt történelmi fordulópont, mert ez volt az első háború, amit szoftverekkel vívtak – igaz, a biztonsági tanúsítványok ellopása akkor még klasszikus kémfilmes stílusban, manuálisan történt.
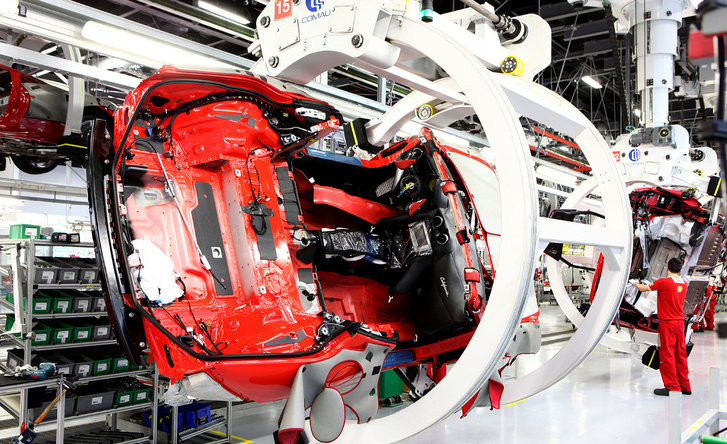
A Stuxnet csodája a precíz felparaméterezés volt, úgy tudták körbefertőzni a világot, hogy máshol csak nehezen okozhatott gondot. Célzottan az ipari gépek logikai vezérlőjét célozta, és egy ilyen PLC irányította az iráni centrifugákat is – ezek szabályozták a nagyon nagy, ugyanakkor rendkívül precízen beállított fordulatszámot, amiben ha eltérés van, akkor a dúsítás sikertelen. A vezérlő dolga a fordulatszám pontos tartása, és a Stuxnet ebbe zavart bele, túlpörgette a centrifugákat, miközben az ellenőrző felületen normál adatokat mutatott. És a vírus kizárólag az Iránban is használt Siemens PLC-ket támadta, azokat is csak akkor, ha a rákötött gépek olyan fizikai elrendezésben voltak, ahogyan az iráni laborban – ezek elrendezéséről egyébként állítólag a labor elnöki látogatásáról készült PR fotók alapján értesültek a vírus készítői. Erről szól egyébként a Zero Days című dokumentumfilm.
A Stuxnet példája mutatja, hogy a hálózatba kötött ipari rendszereknél a biztonság kulcsfontosságú, a közelmúlt rengeteg kiszivárgott kiberakciója után pedig senkinek nem kérdés, hogy mekkora kihívás ez valójában.
Mivel egy komplex ipari rendszernél nem megoldható, hogy a többi hálózattól hermetikusan elzárva működjön – gondoljunk csak a karbantartásra, frissítésre, amikor rádugnak egy külső eszközt – így egyelőre ezen a téren még várjuk a nagy áttörést, a végpontok közötti titkosításoknak jelentős javuláson kell átesnie. Népszerű nézet, hogy a kvantumszámítógépek jelentik majd a megoldást. Röviden és felszínesen arról van szó, hogy az optikai kábelen kommunikáló kvantumszámítógépek a titkosított üzenethez tartozó kulcs minden bitjét egyetlen fotonra (fényrészecskére) kódolják, amit aztán egy közönséges optikai kábelen továbbítanak. Mivel a fotonok olvasására tett kísérlet megváltoztatja a kódolást, ezért a kulcsok titkossága garantálható és ellenőrizhető lehet.
A felmerülő kérdésekre egyelőre nincsenek kész megoldások, így az átállás sem lesz gyors folyamat. Rengeteg olyan terület van, ahol egyelőre elképzelhetetlen a magas szintű automatizálás és gépesítés, de érdemes ezekre készülni, az Ipar 4.0, a mesterséges intelligencia, a big data, az IoT, a blokklánc és a gépi tanulás olyan fogalmak, melyek kéz a kézben járnak, és a bevásárlástól, az egészségügyön át a közlekedésig az életünk minden területére hatással lesznek–már a mi életünkben.
A cikk megjelenését a 4iG támogatta.
